Lee's Summit, MO Residential HVAC & Plumbing Services
LBA Services was started by people just like you who want and insist on high quality and reliable service. In Lee's Summit, MO and throughout the Kansas City area, we treat each family and home as if it were our own. That includes rising to the challenge of being a Hero any time the need calls for extraordinary measures.
From routine maintenance to 24/7 emergency repairs, LBA Services has you covered for all your home plumbing, heating, and air conditioning needs since 1985. The same goes for new and replacement system installations.
Contact Our Lee's Summit Office
Address: 622 SW 3rd St Suite D, Lee's Summit, MO 64063
Phone: (913) 228-3998
Read our reviews below and find out why your neighbors consider us to be their nearby heating and air company and local plumber in Lee's Summit, MO.
Recent Jobs and Reviews in Lee's Summit, MO
Customers say: The reviews exhibit a positive sentiment, with a majority of customers expressing satisfaction with the services provided. The recurring themes include professionalism, expertise, honesty, promptness, and excellent customer service. Customers appreciate the technicians' ability to diagnose and solve HVAC issues, as well as their friendly and courteous demeanor. There are also mentions of transparency, honesty, and providing multiple options to address problems. Negative reviews are minimal and focus on the cost of parts or the need for replacements, but even in these cases, customers acknowledge the professionalism and helpfulness of the technicians. Overall, the sentiment is positive, with customers expressing gratitude and satisfaction with the services provided by LBA.
Our Local Reviews by City
- Adrian, MO (2)
- Avondale, MO (1)
- Basehor, KS (22)
- Bates City, MO (1)
- Belton, MO (32)
- Blue Springs, MO (63)
- Bonner Springs, KS (30)
- Buckner, MO (1)
- Bucyrus, KS (6)
- Columbia, MO (1)
- De Soto, KS (22)
- Dearborn, MO (1)
- Edwardsville, KS (14)
- Eudora, KS (9)
- Fairway, KS (90)
- Freeman, MO (1)
- Gardner, KS (14)
- Gladstone, MO (64)
- Grain Valley, MO (40)
- Grandview, MO (73)
- Greenwood, MO (2)
- Houston Lake, MO (7)
- Independence, MO (177)
- Kansas City, KS (412)
- Kansas City, MO (2815)
- Kearney, MO (3)
- Lake Lotawana, MO (4)
- Lake Quivira, KS (19)
- Lake Waukomis, MO (4)
- Lansing, KS (2)
- Lawrence, KS (19)
- Leavenworth, KS (7)
- Leawood, KS (417)
- Lee's Summit, MO (155)
- Lenexa, KS (589)
- Liberty, MO (105)
- Lone Jack, MO (1)
- Louisburg, KS (5)
- Merriam, KS (20)
- Mission, KS (198)
- Mission Hills, KS (76)
- North Kansas City, MO (10)
- Northmoor, MO (1)
- Oak Grove, MO (12)
- Odessa, MO (1)
- Olathe, KS (606)
- Ottawa, KS (1)
- Overland Park, KS (1412)
- Parkville, MO (185)
- Peculiar, MO (1)
- Platte City, MO (13)
- Pleasant Hill, MO (1)
- Pleasant Valley, MO (4)
- Prairie Village, KS (520)
- Prairie Village New, KS (2)
- Raymore, MO (24)
- Raytown, MO (78)
- Riverside, MO (17)
- Roeland Park, KS (186)
- Shawnee, KS (1010)
- Shawnee Mission, KS (1)
- Smithville, MO (1)
- Spring Hill, KS (12)
- Stilwell, KS (65)
- Sugar Creek, MO (7)
- Weatherby Lake, MO (28)
- Wellsville, KS (1)
- Westwood, KS (29)
- Westwood Hills, KS (17)
Job Locations and Reviews

This is a budding pricing if everything gets done at the same time a we can set the date up this week for the future

Arrive to calibrate a systems refrigerant charge. Previously a field supervisor came out to aid in diagnosing the system. Field supervisor determined that the system is low on refrigerant. Upon arrival connected refrigerant gauges and started reading system refrigerant charge. System appears to be overcharged, based on my readings at this time. Calibrated system and charge to factory specs. Suspect that the metering device for the refrigerant is not working properly. Calibrated system refrigerant charge to achieve a 20° temperature split. Adjusted settings on the thermostat to ensure that the system continues to maintain temperature throughout the day. System is cooling upon departure.

System has a temp split of 14 degrees, indicating a low refrigerant charge. We will be out in the morning to charge the system and once we have info on coil availability we will go from there

I removed side discharge duct work and replaced the condensation drain line completely. Relocate the j trap to outside of the the duct. Reconnect side discharge metal and ran the system to verify that it is not going to leak again. Unit is draining as it should be.

Called to review the maintenance.

Went for a maintenance call today. Tested for static pressure, system is passing. All electrical components are passing for system. Refrigerant levels are passing. Did replace filter, as well cleaned condenser unit. System is up and running before leaving. Thank you for choosing LBA services-Johann

Went for a house not cooling. System are operating properly. Temp split of 21 degrees passing. Did clean condenser unit. Checked charge and refrigerant levels are passing. Ac is working properly and passing for manufacture specifications. Will recommend to get insulation checked and windows. To know whether there any leaks in insulation or windows that causing for home not to cool properly. Since the systems are working properly. Thank you for choosing LBA services-Johann

For this job we talked about replacing 2 shower valves. Customer wants to remodel so he’s thinking he’ll wait till the walls before he decides. If work done credit back 120 trip fee. Send estimates too customer email

Na

I found that the condensation drain was clogged. I blew trap out with water and refilled. It is draining as it should be. I let them know to give it some time to dry out before replacing ceiling tile.

Went for a maintenance today. Tested for static pressure, system is failing when in cool. Did adjust blower speeds for cool. All electrical components are passing for manufacture specifications. Refrigerant levels are within range passing. Did replace filter as well cleaned condenser unit. System is up and running before leaving. Thank you for choosing LBA services-Johann

Estimate
Excellent!

Customer wants to replace broken prv

Arrived to remedy a system that’s unable to keep up in the heat. Upon arrival set system to cooling and system started up as designed. Performed diagnostic on the inside portion and found that the system is operating with a 20 degree split. This is all we ask of air conditioning systems but with how hot it is in the home this can be achieved without proper operation. Went outside and continued diagnostic. Refrigerant levels appear to be where they need to be and electronic components are functioning properly. Went back inside and double checked airflow. Found that when the system was installed the airflow was adjusted but were not set on the correct setting. Made the proper adjustment to the fan speed and checked the refrigerant levels. Calibrated system charge to meet the proper airflow. System is still cooling more than 20 degrees and is handling humidity more efficiently.

B

Est to replace water heater

Today I arrived and checked in with Sherry. The concern was that the rooftop unit that serves the parts department was not cooling. I accessed the roof and discovered that the unit was not cooling due to a high pressure safety switch that had shut down both compressors. The cause of this outage was that cottonwood had completely coated the condenser coil and this raised the pressures in the system. Hose was pulled onto the roof, hail guards were removed and the unit was washed thoroughly to remove the cottonwood. After this was completed the hail guards were put back on and the unit was checked for proper cooling functions. The unit returned to normal function. While there was a hose on the roof the other rooftop units on the same roof were quickly washed. Their maintenance is coming up so they were not washed thoroughly just enough to remove the cottonwood and prevent a shut-down. The showroom had a high humidity load and was uncomfortable. The thermostats for the s

Installed new indoor coil

Arrived to remedy a system that is intermittently cooling. Performed diagnostic and found that the capacitor in the condenser is failing. This part is covered by a parts and labor warranty. Recommended installing a compressor start kit to reduce the stress of system start up from the capacitor and compressor. Homeowner declined the compressor start kit at this time. Replaced the failing capacitor and tested system operations. System is functioning at this time.

Arrived for water leaking in furnace room. Upon inspection I found that the water heat next to furnace was leaking. The system itself has good pressures and charge. There is also a 20-21 degree temp split, which is great. I rinsed coil clean. There was lots of condensation on the duct work. I recommend adding some vents into the furnace room. System is running upon departure. Thanks for choosing LBA.

Drain clearing.

EST to jet
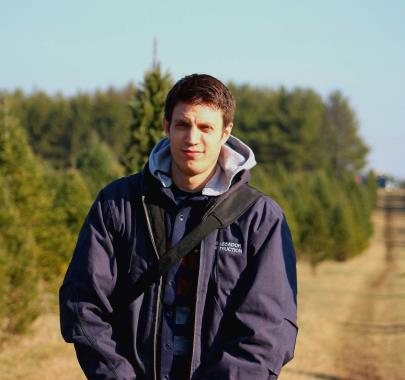
For today, I was checking in the system that wasn’t cooling efficiently. When I arrived, it was definitely low on refrigerant so I added refrigerant with UV seal. I also added refrigerant line caps and cleaned out the unit. All levels on refrigerant and temperature split now look good and with the UV dye in there we will know if there’s a leak if the system falls behind again we can come look for it. Ended up adding nearly 3 pounds of refrigerant.

Today the split-system that serves the office was checked. The concern was that it was not cooling well. I checked the temp split and the cooling was in range at 77degf in and 59 degf out. The condenser on the roof was checked for proper airflow and guages were attached to check the pressures against the manufacturer’s charging chart. What was discovered was that the condenser coil was covered with cottonwood. It was cleaned today and the temperatures were rechecked. The air filter was also replaced using a client supplied filter (1) 20x25x1. It was not packed however it did need changed. The system responded to the cleaning with more airflow through the condenser and it was rejecting more heat. The refrigerant level is correct. The condenser was reassembled and my findings were relayed to the client. Thank you, Jon

Customer declined at this time. Estimate emailed.
Excellent service
Excellent service
We have been in our home for 5 years and Graham is as the first person to ever check the static air. In under an hour he explained things other companies couldn’t for years.
Fantastic
Good job
We’re delighted to hear about your recent experience with us and we’re so pleased that you recommend our services.
Great service
We’re delighted to hear about your recent experience with us and we’re so pleased that you recommend our services.
JJ was quick and efficient. He was very polite. He explained everything he was doing and the outcome. This was my first experience with LBA and I will use again,
I felt that they were very honest and very thorough.
Very nice also professional Took care of air conditioner and explained thermostat thoroughly. Also left the instructional paper work. Did not have any on one that replaced mine This included the new air conditioner Courteous and very helpful to person learning with him. He gets an A for taking the time to make sure I knew what I was doing Being a problem child with your company he took. Care of it. Thank you